- Title
-
Getting back on track: transforming the supply chain at a major rolling stock manufacturer
- Section
- Case study
- Summary
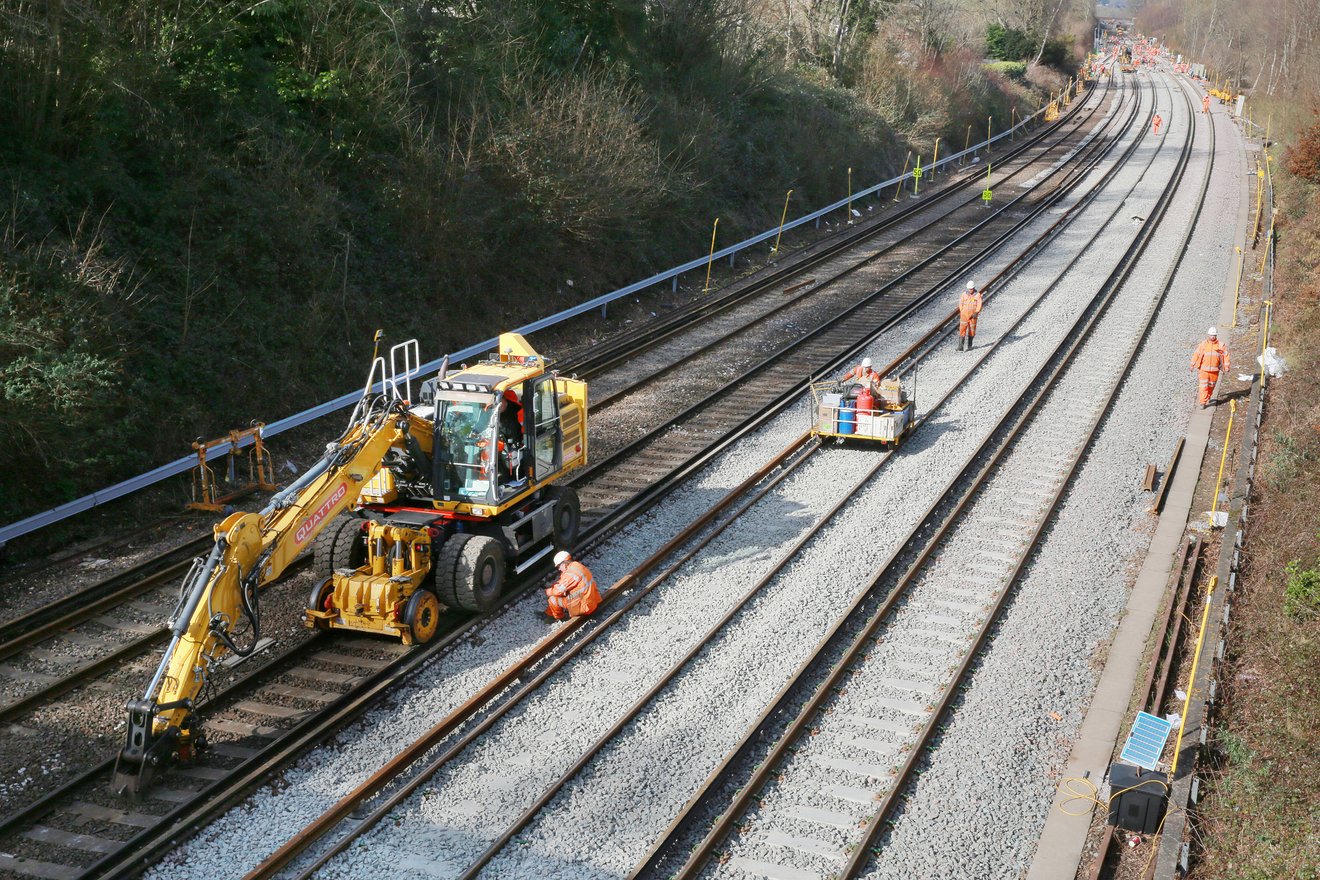
A major rolling stock manufacturer had recently opened a greenfield manufacturing facility in Northern England, a major success for the industry, region and manufacturer. However, significant material management challenges risked deadlines for new trains being missed, resulting in hefty penalties.
With material availability (the percentage of items available for use on the production line on a day-to-day basis) well below target, the build schedule was falling behind the plan. With deadlines looming, Efficio was engaged to urgently identify and resolve the issues.
Efficio quickly identified the underlying causes and took a number of actions to address them, with rapid and significant results. Material availability increased by nearly 50%, meeting the client’s target and making a major contribution to getting the build schedule back on track.
Background
By opening its new train manufacturing facility in Northern England, the client was ‘bringing train building back home’ and creating over 700 jobs. The initial focus of the plant was on fulfilling the client’s first major contract to build 173 trains.
The trains were to be designed overseas and built in England by experienced local manufacturing staff, augmented by staff from the client’s international locations to provide knowledge transfer in the initial stages. However, a lack of specific supply chain expertise meant the right parts were not always available at the right time for the production line, causing shutdowns and delays in production.
With hefty financial penalties for missing delivery deadlines, any delays had serious and significant consequences. Efficio was engaged to urgently address and resolve the issues causing the delays.
It quickly became apparent that a key issue was the lack of good data, which made effective supply chain management impossible. Issues with the plant’s ERP system meant there was no effective Material Requirements Planning (MRP) system in place. This was exacerbated by different stakeholders having different assumptions about the relevant supply chain processes, which made it very difficult to determine the root cause of the delays.
Other issues included duplication of parts (which meant the same part could have multiple part numbers), and problems with the movement of parts between offsite and onsite warehouses, due to difficulties in forecasting future requirements. The warehouse and material control staff had to spend hours relabelling and reconciling different part numbers to prevent ‘false shortages’ on the production line.
Efficio’s work provided the client with a clear understanding of what was causing the delays, and what needed to be addressed. The initiatives they put in place succeeded in resolving the issue of material availability in a very short timeframe, and in a high-pressure environment.
Approach
- Augmenting the client staff by placing Efficio staff in key client line roles such as head of supply chain and head of material control to inject immediate supply chain expertise and knowhow; this was in addition to an on-the-ground Efficio project team
- Building and deploying a series of bespoke tools to address the data issues, including a ‘mini-MRP’ system that matched production requirements with material availability, and calculated availability for all trains over a 12-month timeframe. This allowed the material control team, for the first time, to identify and resolve potential shortages before they became an issue. Efficio also developed tools to address the issues with stock transfers between offsite and on-site warehouses
- Optimising inventory by creating and deploying a category-based process for buying material and moving almost 40% of daily picks to a Kanban system, freeing up significant resources
- Clarifying roles and responsibilities for the material master data team, which led to significant improvements in data management. Efficio also developed a bespoke tool to manage the issue of duplicate part numbers
- Developing a KPI pyramid with each tier tied into the one above, to ensure all functions were working towards the same goal
Results
Efficio’s work provided the client with a clear understanding of what was causing the delays, and what needed to be addressed. More importantly, the initiatives they put in place succeeded in resolving the issue of material availability in a very short timeframe, and in a high-pressure environment.
Material availability increased nearly 50%, from 65% at the start of the engagement to 95% - meeting the client’s target and helping to mitigate the huge costs of line shutdowns.
As well as delivering the key objective, the engagement also provided a range of ongoing benefits to the client.
The bespoke tools Efficio developed freed up significant amounts of time for the material control and warehousing teams, allowing them to focus on resolving issues in other areas – for example, reducing the time needed for the warehousing team to forecast future requirements from 1.5 hours to less than ten minutes.
The tools, along with the KPI process Efficio introduced, also provided key management information, which was not previously available. This information informed Efficio’s fact-based approach and continues to be used by the plant’s management team to identify potential problems and the solutions to address them.